In today’s fast-paced work environment, organizations are constantly seeking ways to enhance efficiency and productivity. One of the most effective methodologies employed by companies worldwide is the 5S framework. Originally developed in Japan as part of the Lean manufacturing philosophy, 5S emphasizes organizational skills aimed at creating and maintaining a clean, orderly, and efficient workspace. By implementing the 5S principles, businesses can not only streamline operations but also foster a culture of continuous improvement.
The 5S methodology consists of five key pillars: Sort, Set in order, Shine, Standardize, and Sustain. Each pillar plays a crucial role in transforming the workplace into a more productive environment. Not only do these principles help in eliminating waste, but they also promote safety and employee morale. As organizations strive for excellence, understanding and adopting the 5S framework can be a game-changer.
In this article, we will explore the intricacies of the 5S methodology, addressing common questions and providing insights into how businesses can effectively implement these principles. Whether you are a small business owner or part of a large corporation, the 5S framework can be tailored to suit your specific needs and objectives.
What is the 5S Methodology?
The 5S methodology is a systematic approach to workplace organization and standardization. The name "5S" is derived from five Japanese words, each corresponding to a step in the process:
- Sort (Seiri): Distinguishing between necessary and unnecessary items and removing the latter.
- Set in order (Seiton): Organizing and arranging tools and materials for easy access and use.
- Shine (Seiso): Cleaning the workspace and maintaining cleanliness to ensure a safe environment.
- Standardize (Seiketsu): Creating standards and protocols for maintaining the first three S's.
- Sustain (Shitsuke): Developing a culture of discipline and commitment to continue adhering to the 5S principles.
How Can 5S Improve Workplace Efficiency?
The implementation of the 5S methodology can lead to significant improvements in workplace efficiency. Here are a few ways in which 5S contributes to enhanced productivity:
- Reduction in Wasted Time: By sorting and organizing tools and materials, employees spend less time searching for what they need.
- Improved Safety: A clean and organized workplace reduces the risk of accidents and injuries.
- Enhanced Morale: Employees feel more motivated and engaged in a tidy and well-structured work environment.
- Better Quality Control: Standardized processes lead to consistent results and higher quality outputs.
What Are the Key Steps to Implementing 5S?
Implementing the 5S methodology requires a structured approach. Here are the key steps to successfully adopt 5S in your organization:
- Educate Your Team: Conduct training sessions to familiarize employees with the 5S principles.
- Assess the Current State: Evaluate the existing workspace to identify areas that require improvement.
- Develop an Action Plan: Create a detailed plan outlining the steps needed to implement 5S.
- Engage Employees: Involve team members in the implementation process to foster ownership and commitment.
- Monitor Progress: Regularly review the progress of 5S implementation and make necessary adjustments.
Can 5S Be Applied in Any Industry?
Absolutely! The versatility of the 5S methodology allows it to be applied across various industries, including:
- Manufacturing: Streamlining production lines and reducing waste.
- Healthcare: Enhancing patient safety and operational efficiency.
- Office Environments: Improving organization and workflow.
- Retail: Optimizing inventory management and customer experience.
What Challenges Might Arise When Implementing 5S?
While the benefits of 5S are clear, organizations may face challenges during implementation. Some common obstacles include:
- Resistance to Change: Employees may be hesitant to adopt new processes.
- Lack of Commitment: Without leadership support, 5S initiatives may falter.
- Inadequate Training: Insufficient knowledge of 5S principles can lead to ineffective implementation.
How Can Organizations Sustain 5S Practices Over Time?
To ensure the longevity of 5S practices, organizations can take the following steps:
- Regular Audits: Conduct periodic assessments to ensure adherence to 5S standards.
- Ongoing Training: Provide continuous education and support to employees.
- Cultivating a 5S Culture: Encourage a mindset of improvement and accountability throughout the organization.
Conclusion: Is 5S Worth Implementing?
In conclusion, the 5S methodology offers a powerful framework for organizations aiming to enhance efficiency, safety, and employee morale. By implementing the principles of Sort, Set in order, Shine, Standardize, and Sustain, businesses can create a more productive and organized workplace. The initial investment of time and effort in adopting 5S practices can yield substantial long-term benefits, making it a worthwhile endeavor for any organization. If you are looking for ways to improve your business operations, integrating the 5S methodology might just be the solution you need.
Exploring The Allure Of Kaitlan Collins In A Bikini
Discovering The Allure Of Vegas: Its Charm, Culture, And Entertainment
Alysha Clark: Love, Life, And Marriage

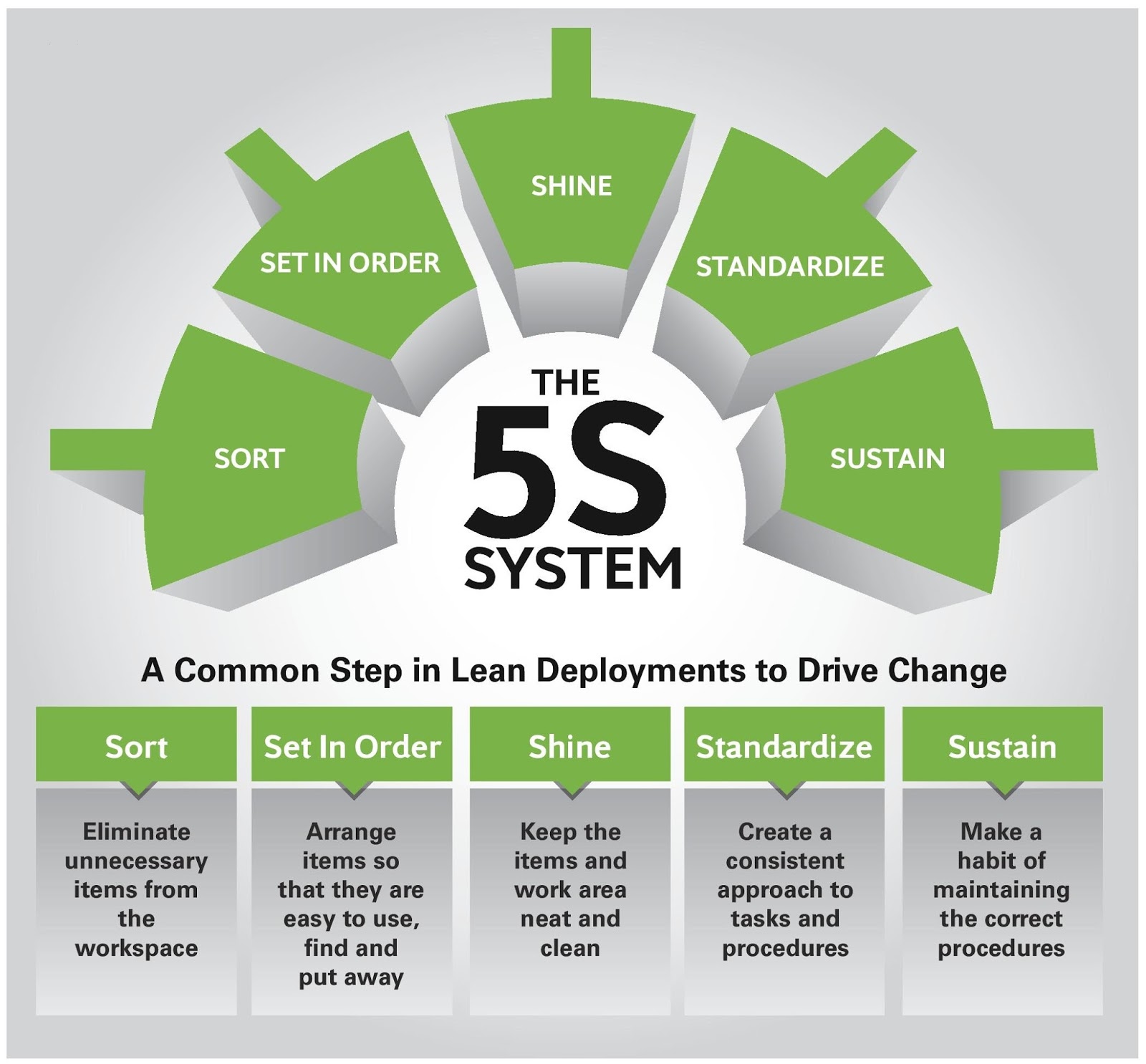